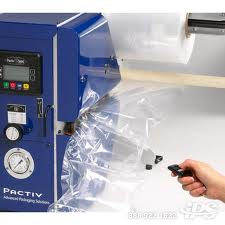
A leading manufacturer of consumer electronics had been using Ranpak table-top units to create cushioning material at two replacement part facilities. The Ranpak units convert fan-folded paper into crumpled void-fill. The company had been spending 850K per year on the dunnage and felt they were paying too much. That prompted them to investigate inflatable, air-cushioning systems. They contacted IPS Packaging to see what they would recommend as a viable packaging solution.
-
Spending over 850K per year on dunnage
-
Inefficient packaging system/Desired better performance
-
Improved performance
-
Cost savings
-
Reduced freight costs
-
Air cushioning weighs less than paper void fill
The customer wanted a lower “in the box” cost. Analysis of air pillow benefits (cost, weight, freight) showed them that this was the way to go. The company also took a look at FP Int’l and Automated Bag air pillow systems. The determination was made that IPS Packaging's Pregis material/systems yielded superior performance coupled with cost benefits—35-40% annual savings vs. the Ranpak system.

Pregis designed a shared delivery system for both the Air Speed 5000 and the HC unit. Each delivery system services a “quad” or four-station packaging table. There were a total of nine quad set-ups in the East coast facility which means that nine of each unit were sold into that facility. The west coast plant has been supplied with six Air Speed 5000 and one HC unit. The Airspeed HC unit is used to produce a bottom cushion and/or any blocking/bracing or interleaving that is needed—depending on the part. TheAir Speed 5000 creates void-fill pillows.
In addition to a reduction in packaging costs, the customer also has benefited from reduced freight costs due to air cushioning weighing less than the paper void fill.